整车路噪仿真及优化技术应用
摘要:系统介绍整车道路噪声仿真及优化技术在车辆设计开发阶段的应用,包括路噪目标值设定方法、高精度整车模型搭建、逆矩阵法计算6自由度载荷、整车路噪仿真、路噪问题诊断FS方法、路噪优化案例。提出系统诊断路噪问题的“FS”方法,运用此方法可系统地对路噪问题分析诊断,快速定位问题点。给出“FS”法在某车型路噪问题诊断案例,验证其有效性。随着国内汽车消费市场越来越庞大、越来越成熟,消费者对车辆舒适性要求也是越来越高。车辆路噪控制水平一直是国内外各大主机厂非常关注的一项NVH 性能,它直接影响到乘用车乘坐舒适性。尤其对于EV 车型,因为缺少了发动机的遮掩效应,其路噪问题更加凸显。国内主机厂在设计阶段对路噪性能关注得比较少,究其原因是设计阶段路噪开发能力有限。国内路噪开发重点在试验样车调 教,样车调 教过程中涉及到的问题点往往包含车身骨架、车身大板件、前后副车架、摆臂、连接衬套等,但这些部件后期进行设计变更难度极大,如车身结构设计变更会影响到周边搭接部件以及会带来一些布置冲突问题,底盘衬套刚度的调整又会影响到车辆操稳性能。因此在设计阶段建立路噪分析、预测、优化的方法显得尤为必要,应力争在设计阶段解决路噪问题。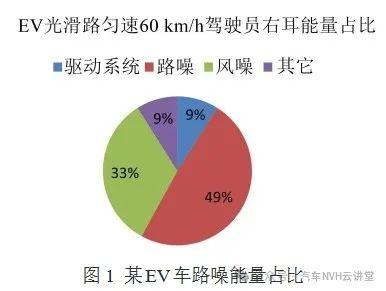
本文介绍了设计阶段搭建高精度路噪仿真模型的关键点、路噪目标值设定方法及轴头载荷获取方法,并提出了路噪诊断“FS”方法,给出了某款车型路噪诊断优化案例。本文仿真模型基于有限元理论,路噪分析频率限定为20 Hz~300 Hz。1 路噪仿真及问题识别方法
设计阶段路噪仿真 主要是整车及子系统路噪相关仿真分析优化。子系统仿真分析主要是对路噪影响较大的部件进行模态分析,使模态合理地分布,此工作国内开展相对成熟,本文不做过多介绍。整车路噪仿真分析优化一般从TG1 阶段开展,至TG2阶段结束,涉及工作包括路噪分析目标值设定、整车路噪仿真模型搭建、路噪载荷获取、路噪分析计算、诊断、优化。1.1 整车路噪有限元分析理论介绍
整车路噪有限元分析理论基础是声振耦合有限元法,搭建整车和乘员舱声腔有限元模型,耦合整车和声腔模型求解驾驶员耳朵位置声压级。用空气单元形函数及声学波动方程,可导出声腔有限元状态方程(1),类似可导出结构振动有限元方程(2)
式(1)中:[ Mep ][ Cep ][ Kep]ρ[ Re]T 分别为空气质量矩阵、空气阻尼矩阵、空气刚度矩阵和结构声学耦合质量矩阵。{ pe }为空气单元节点声压向量,Ue 为节点位移向量。式(2)中,[ Me ]、[ Ce ]、[ Ke ]、{ Fe }分别为结构质量矩阵、结构阻尼矩阵、结构刚度矩阵和结构外激励,{ F }Per为界面声压向量。将乘员舱声腔和整车有限元方程联立得到结构振动-声腔耦合有限元方程组,求解此方程组可以得到驾驶员耳朵位置路噪。1.2 路噪目标线设定
设定路噪分析目标值时应该对所采用的试验场、路面、车辆运行速度及状态、测量位置做出明确的说明,因为这些因素对路噪影响很大,影响到路噪目标值的设定。路噪评价可使用标准试验场内粗糙沥青路、光滑沥青路或刻槽水泥路,国内主机厂通常根据企业标准选择相应路面进行评价。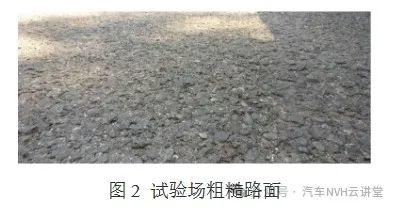
目标值可以在线性谱中设定也可以在1/3 倍频程内设定,本文采用线性谱方式。目标值设定要综合标杆车型路噪水平、设计车型路噪性能定位、路噪控制趋势等因素。如某车型以车辆60 km/h 在通县试验场粗糙路匀速行驶时驾驶员右耳声压级进行路噪评价,目标线设定如图3所示。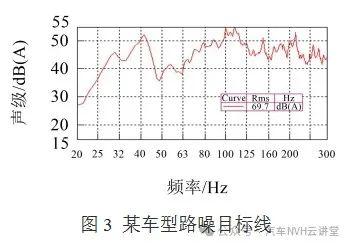
1.3 高精度整车模型搭建
车身、底盘甚至动力系统对路噪都有影响,为了准确计算出这些部件的影响,分析模型要包含这些部件,故需要搭建整车模型进行分析计算,某项目搭建的整车模型及乘员舱内声腔模型如图4和图5所示。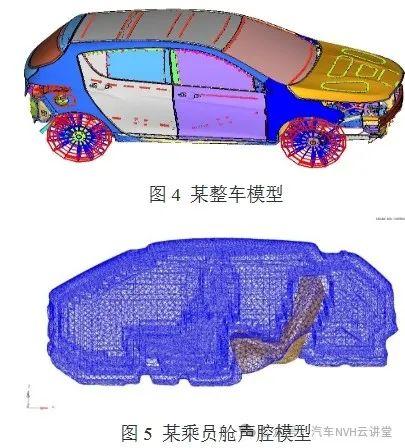
整车模型复杂度高,其精度对路噪分析结果影响很大,为了保证模型精度,整车建模过程需要注意以下问题:Ø 整车模型质量需要与设计值标定,误差小于15 kg;Ø 乘员舱声腔与周围壁板贴合度要好,否则壁板振动无法传递至声腔;Ø 底盘与车身连接衬套动刚度和阻尼与设计值严格对应;某车在北京通县试验场光滑沥青路面以60 km/h 匀速行驶,采集驾驶员右耳声压级评价路噪,图6为路噪实测值和仿真值对比,主要峰值在仿真模型都得到了反映,并且声压级差值小于4 dB,精度满足工程要求。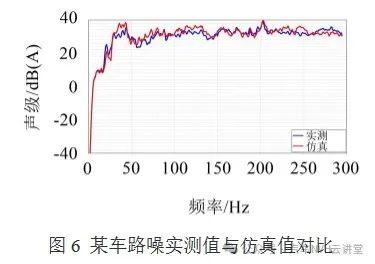
1.4 路噪载荷获取方法
整车级别路噪分析载荷可以是轴头载荷也可以是路面不平度激励,如果采用路面不平度激励需要搭配模态轮胎和虚拟试验场使用,本文主要介绍轴头激励的获取方法。悬架系统是多输入多输出的线性系统[5],输入X 是轴头对转向节的激励载荷,输出Y是转向结上测点振动,H(ω)是载荷和振动之间的传递矩阵,对于稳定的线性系统,如果输入是随机并且部分耦合的,系统的响应也具有随机性和耦合性,输入和输出功率谱密度矩阵的形式分别表达成Gxx(ω)和Gyy(ω),输入和输出之间的关系如下
式中H(ω)H 是H(ω)共轭转置矩阵,当输出Gyy(ω)和传递矩阵H(ω)已知后,输入Gxx(ω)可以计算出来。在试验车每个转向节上选取4 个测点,试验车进行路噪试验,采集每个测点振动加速度,可获得转向节测点加速度输出矩阵Gyy(ω),通过整车有限元模型计算得到传递矩阵H(ω),轴头作为激励点其6自由度载荷可通过式(4)得到。某车选取的左前悬架转向节4个测点位置如图7(黄色)圆圈所示。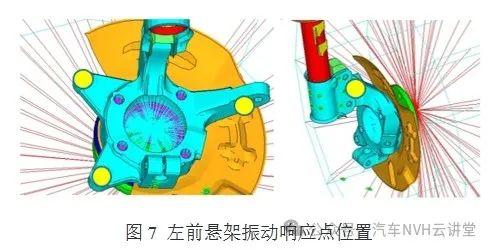
具备整车模型和载荷后,可通过仿真计算得到路噪。路噪仿真分析常见问题是驾驶员或乘员耳朵位置声压级曲线在某个频率未达到目标,由于路噪问题涉及的子系统多、载荷传递路径多,所以问题识别起来非常复杂。本文提出一种“FS(Fast System)”诊断方法,使用此方法可以快速地、系统地诊断出路噪问题,此方法使用过程如图8所示。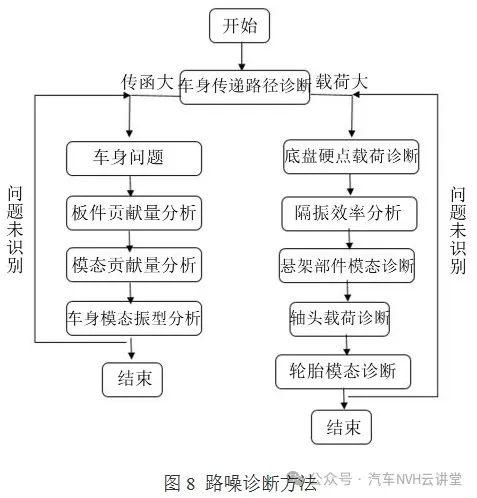
2.1 问题描述
某车型在路噪开发过程中,以通县试验场光滑沥青路作为评价道路,车速60 km/h,评价驾驶员右耳计权(A)声级,以标杆车型相对应的测试结果作为目标值,仿真结果表明开发车型驾驶员右耳声级在90 Hz超过目标值,如图9所示,需诊断及优化。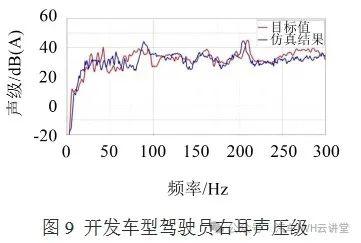
2.2 问题诊断
使用路噪诊断FS方法,先进行车身侧传递路径分析,之后进行车身侧NTF、模态分析,最后进行底盘侧隔振率、悬架模态分析,最终锁定90 Hz路噪问题原因,具体诊断步骤如下:对此车进行车身侧传递路径分析,图10可知1 510(右前减振器安装点)+Z路径贡献度最大,此传递路径贡献度大可能是此路径载荷过大引起的,也可能是此路径车身NTF(噪声传递函数)过大引起的。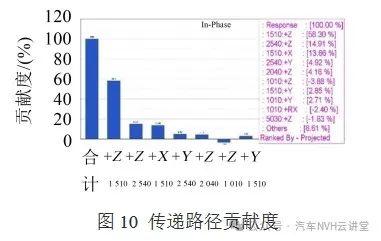
图11是各激励通道载荷图,虽然2 540(右前摆臂前安装点)+Y 通道载荷最大,但此传递路径贡献度不高,说明此路径NTF 很小,这点从图12各通道NTF幅值图中可以得到证明。1 510(+Z)载荷明显高于除2 540(+Y)的其它路径,表明底盘侧存在设计问题导致载荷传递不均。图12可见车身侧1 510(+Z)NTF幅值在59 dB,符合车身对NTF的一般要求,但仍需进一步确认90 Hz 此路径NTF 是否有峰值,如果没有峰值,则可确认车身不是导致路噪90 Hz 峰值的原因。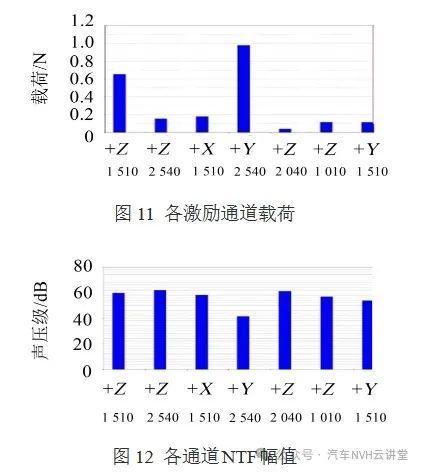
计算1 510(右前减振器安装点)+Z向NTF,结果如图13所示,可知90 Hz频率位置曲线存在峰值,说明此频率车身可能存在共振。90 Hz 模态如图14所示,振型模式及NTF 的PSA 诊断结果均表明对车内声压级影响最大共振位置为前风挡流水槽区域。图15显示了右前减振器顶部衬套主被动侧加速度振动级,可见衬套在整个频域内基本没有隔振能力,此衬套Z向动刚度参考标杆车试验而来,设计值10 000 N/mm,和数据库中此位置衬套刚度对比明显偏高,数据库中此衬套Z 向动刚度设计值一般在1 500 N/mm左右,动刚度偏高可能是隔振能力不足的原因。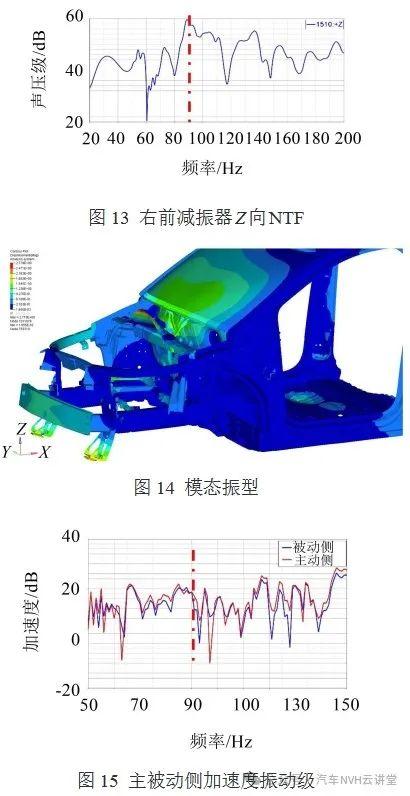
前悬架90 Hz存在模态,如图16所示,左右减振器的主要振动模式是沿简杆方向上下运动。(1)前悬架存在90 Hz 模态,此模态运动模式为沿着减振器简杆方向上下运动,此模态会加大减振器衬套主动端振动;(2)前悬架顶部减震橡胶刚度较大,没有起到振动衰减作用,造成传递到车身的载荷较大;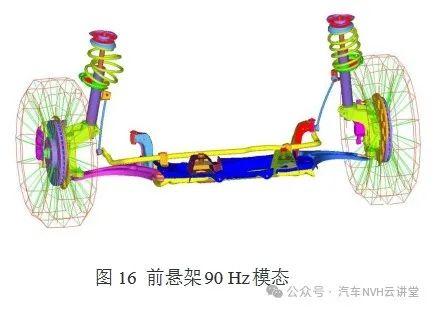
(3)车身90 Hz 模态前风挡和流水槽相对位移大,与声腔耦合,产生NTF峰值,加剧了路噪。2.3 方案及效果
优化前减振器顶部衬套刚度至数据库中某款车型数据,如表1所示。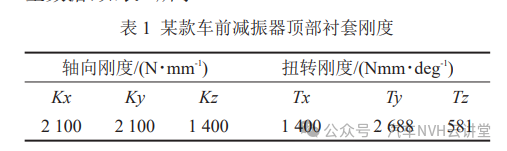
方案1效果如图17所示,路噪响应曲线在90 Hz位置降低了3 dB,基本达到目标要求。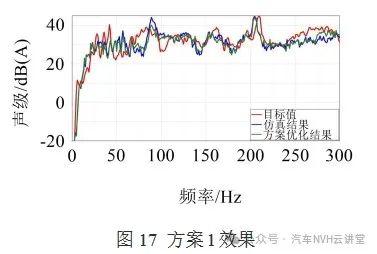
在方案1基础上优化流水槽加强支架,加强2号支架,增加3 号支架,3 号支架厚度1.2 mm,如图18所示。优化后路噪响应曲线在90 Hz 位置相对于方案1降低2 dB,优于目标要求,结果如图19所示。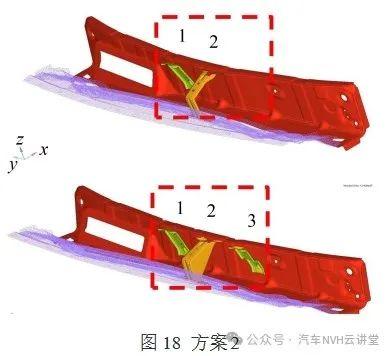
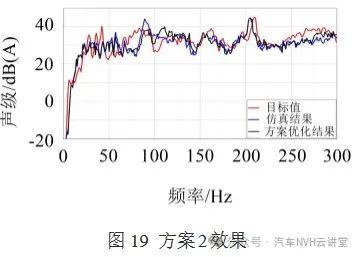
本文系统介绍了整车路噪仿真和优化技术在车辆NVH 开发设计阶段的应用,提出了路噪诊断的FS方法,并通过路噪诊断优化案例验证了FS方法有效性。本文所介绍的路噪相关理论、方法,不仅可以用于乘用车NVH 性能开发,也可以用商用车NVH性能开发,为相关工程师提供借鉴参考。作者:陈 钊1,霍俊焱2,吴星晨2,邓江华2,王海洋2
1.东风柳州汽车有限责任公司
2.中国汽车技术研究中心有限公司
获取原文请点击文末阅读原文。
【免责声明】本文来自网络,版权归原作者所有,仅用于学习等,对文中观点判断均保持中立,若您认为文中来源标注与事实不符,若有涉及版权等请告知,将及时修订删除,谢谢大家的关注