你可能并不一定真正知道电动汽车是如何研发和制造的?下面将详细介绍电动汽车的研发和制造全过程,欢迎收藏学习!
一、策划阶段
在汽车新产品开发之前,通常要对产品和市场进行调查,了解市场需求和新技术的发展状况,同时结合公司自身的特点、技术水平、设备状况、工艺水平、生产能力和实力等状况进行分析,必要的时候还要走访客户、考察配套商或者进行必要的试验测试等工作。这一阶段必须要确认新产品的技术状态、产品档次、产品配置、目标成本以及预期售价、合理利润等。这些都是产品开发的初期资料和基本依据。市场调研是为了确定产品的预期市场占有率,同时也是为了全面了解市场对该类产品的功能、性能、安全、寿命、外观等方面的需求。技术调研包括对目前市场上同类产品的技术水平,所使用的新技术、新材料和新工艺等进行预测。从企业的生产经营角度,进行新产品开发的可行性分析,掌握本企业的技术来源和技术优势,对产品的开发周期和开发费用等投资作预测,对该产品的产量和盈利能力作预测,编写产品开发可行性报告。评审通过后列入企业产品开发计划,然后编写产品开发任务书。任务书一般包含产品设计和立项的依据、产品的用途和使用范围、产品的总体方案概述、关键性技术方案、总体布置及主要结构概述、基本的技术参数和性能指标等等。设计阶段主要是指通过设计确定总体方案、造型方案,进行设计计算,绘制设计图纸,编写设计文件,必要时还需要进行试验和设计评审等,整车设计一般分为如下步骤:对产品和市场进行调研,了解市场需求和新技术的发展状况,提出准确的市场预测和技术可行性报告,企划部门根据可行性报告,制定项目概念,包括产品车型基本参数、车身样式、同类车型、开发周期、竞争优势、生产地、生产纲领等项目立项的战略文件,成立项目组,启动项目开发。
概念设计阶段确定整个汽车产品的目标定位,确定整车、各大总成的性能参数,制定各大总成设计任务书,规定设计控制数据,完成可行性研究报告。概念设计是汽车设计中最重要的阶段,许多整车参数都在此阶段确定。基于CAE技术及大量经验和试验数据的整车数字化仿真体系,可以模拟整车在不同路况下的实际响应,为各零部件的精确CAE分析提供载荷条件,从而进行复杂的非线性动力学分析、关键部件疲劳寿命分析、整车NVH分析。主要工作内容为确定总体方案、造型方案,设计计算,绘制设计图纸,编写设计文件,内外油泥模型冻结。这标志着前期整车开发结束和项目工程开始正式启动;产品的技术方案的可行性分析和总体工艺可行性分析结束。这一阶段的主要任务是制定设计方针,明确目标,确定是全新产品设计还是改型设计,是自主设计还是反求设计等。明确最基本的技术要求后,还要了解国家在汽车产品的技术方面的先进性、产品的系列化和生产方式方面的具体要求,同时收集国内外的资料,进行使用调查、生产状况调查以及同类产品的结构分析,通过整车结构和外形设想,制定产品的开发设计原则。这一阶段主要是正确地选择整车和各总成的结构形式以及主要的技术特性,确定性能参数,形成整车概念,并进行总体布置和选型工作,编制设计任务书。主要包括以下内容:总布置设计时要求将汽车各个总成及装载的人员或货物安排在恰当的位置,以保证各总成运转相互协调、乘坐舒适或装卸方便,可确定汽车的主要尺寸和基本结构。效果图用来表现汽车造型效果。总布置图完成后,造型设计师根据总布置设计确定的电动汽车尺寸和基本形状,勾画出汽车的大体形象,或绘制构思草图,或绘制彩色效果图。可根据需要制作缩小比例模型。比例模型是在彩色效果图的基础上更进一步表达造型构思,更具有立体形象,更有真实感,要求各部分比例严格、曲线流畅、曲面光顺。缩小比例的模型还可以用于风洞试验,用来确定空气动力学特性。其内容包括:任务来源、设计原则和设计依据;产品的用途及使用条件;汽车型号、承载容量、布置形式及主要技术指标和参数;各总成及部件的结构形式和特性参数等。在汽车造型审定后,就可以着手进行汽车结构设计,确定整车、部件(总成)和零件的结构,包括各项参数计算,确定总体配置,确定各部件总成所在的位置和连接方式等等。
这一阶段的工作取决于汽车的性能目标,关键在于建立完善的分析方法和评价策略,主要包括以下分析内容:
目的在于提高产品的被动安全性能,通过正面、侧面、后面、翻滚等各种实车安全性能方面的模拟分析,在产品设计阶段及时发现产品被动安全性能方面的缺陷,提出改进措施。NVH性能是评价车辆舒适性的重要指标,直接关系到产品的市场形象。NVH分析有助于匹配产品结构中各子系统的振动频率特性,合理分布各子系统的振动频率和振型,以消除振动过程中的耦合现象 ,从而改善产品的振动特性,降低产品的噪音,提高产品的舒适性能。在工程样车试制之前,基于多柔体系统理论,解决汽车机械系统设计和动态性能的优化设计问题,将车辆作为一个完整的控制系统进行分析研究,可以建立整车动力学模型,并针对操纵稳定性、平顺性和制动性等性能进行虚拟试验场动态仿真分析,并输出标志整车动态性能的特征参数,制定优化策略。流体分析在汽车工业中主要考虑车外流场对汽车的阻力和升力、车内空调系统通风口的设计、发动机舱的散热、制动系统的散热等,考察整车外形是否流畅,空调系统是否可以快速调节车内所有地点温度,发动机舱和制动片是否散热良好等。在产品设计阶段就可以预测产品的空气动力学特性,确保产品制造出来后符合设计时的空气动力学的要求。
通过合理地分配结构中的各种载荷,从而改善其疲劳耐久性能,提高产品的可靠性能。疲劳寿命设计需要了解产品的使用环境。疲劳耐久性分析包括悬挂组件强度、车门强度、引擎盖强度、行李箱盖强度等。
冲压成形仿真有助于确定产品的可制造性,优化冲压方向,工艺补充,坯料估算和排样。它可以在设计阶段预测产品冲压成形中可能出现的质量缺陷(如起皱、开裂等), 进而对产品设计进行优化, 以消除成形缺陷。工作图设计是指在技术设计的基础上,完成在试制或生产过程中加工、装配、销、生产管理及随产品出厂使用的全部图样和技术文件。每个部件、件及其图纸都给定一个编号,以便于对全部图纸进行管理。试制试验阶段是产品由图纸走向实践的过程,进行样机试制试验并进行小批试制,验证产品图样、设计文件和工艺文件、工装图样的正确性;验证产品的适用性、可靠性和安全性,并完成产品的鉴定。通过小批量试制,进行产品的各种形式试验和试销,确认产品的性能和适应性。样机试制是指根据设计图样生产零部件,进行样机组装试制。汽车的样机试制不仅是按汽车零部件图纸生产,还需要对生产所用到的一些辅助模具、检具进行设计,包括编制工艺文件和制作必要的工装设备。是快速成型(也称快速原型)制造技术(Rapid Prototyping & Manufacturing,样件可以用作CAD数字模型的可视化、设计评价、干涉检验,甚至可以进行某些功能测试。样机试验是对电动汽车的设计和产品进行验证,以保证产品的结构和安全。样机试验是多 方面的,目的是为了验证产品的可靠性、安全性,并进行技术鉴定。整个试制试验过程也是汽车设计从理论走向实践的过程,试制试验的主要工作是进行样车试制,掌握整车和部件的结构工艺性,发现整车在装配中发生的问题并及时协调解决。
- 整车的试验和验证与整车开发的各个阶段总是相互伴随着:
- 设计开发阶段伴随有数字样车的数据仿真验证分析、骡子车的专项性能试验、FT(功能)样车的各项功能性验证和车身相关试验;
小批试制是在样机试制试验的基础上进行的,它的主要目的是考核产品的工艺性,验,证正式生产全部工艺文件及工艺装备质量,并进一步验证产品的性能、结构和经设计改进后的产品设计文件及图样的正确性和合理性。小批量试制完成以后,提交经过修改、改进并最终通过评审的设计资料、工艺文件和全部图样,最终形成完整的产品文件。
比亚迪和特斯拉都是知名的电动汽车制造商,其制造流程都具有高科技含量和复杂性。
比亚迪和特斯拉的制造流程都包括设计、生产和测试三个主要阶段,但是特斯拉采用了更加先进的自动化生产设备和数字化制造技术,使得生产效率更高,产品质量更加稳定。
比亚迪和特斯拉的设计理念也有所不同,比亚迪采用了传统的电动汽车组装方式,而特斯拉则采用了一体化设计思想,使得整车性能更加优越。无论是比亚迪还是特斯拉,都非常注重质量和性能的控制,都采用了严格的测试和质量控制程序。
下面就让我们来揭秘比亚迪和特斯拉的电动汽车制造流程。
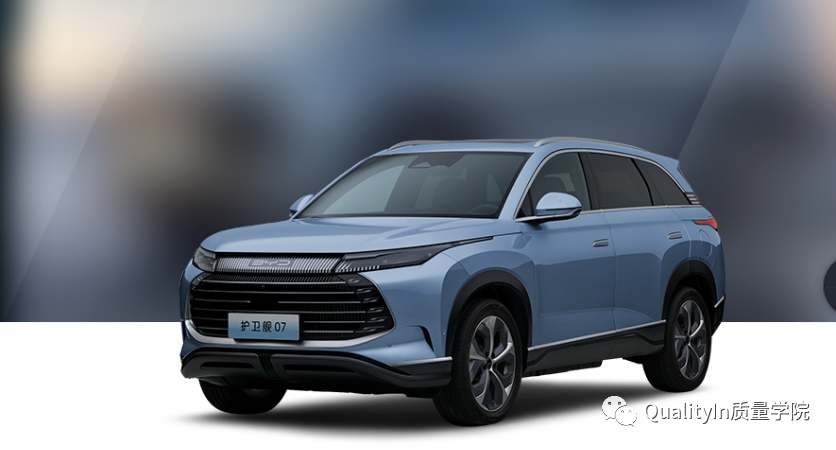
一、比亚迪的电动汽车制造流程
比亚迪是一家中国的电动汽车制造商,其生产线主要位于深圳、东莞和陕西等地。比亚迪的电动汽车制造过程包括设计、生产和测试三个主要阶段。
1、设计阶段
比亚迪的电动汽车设计过程包括外观设计和内部结构设计。外观设计主要包括车身尺寸、形状、颜色等,内部结构设计则包括各种电路板的布局、电池的安装位置、屏幕的安装等。在设计阶段,比亚迪需要考虑到各种因素,如人体工程学、电池寿命、防水性能等。
对于外观设计,比亚迪雇用了全球著名的工业设计师并使用各种计算机辅助设计软件来设计汽车的外观。比亚迪的设计师会根据市场研究和用户反馈来优化设计。
对于内部结构设计,比亚迪需要考虑到各种电子元器件的布局和互相之间的影响。电路板的设计是整个生产过程中最为关键的一环,需要经过多道工序才能完成。设计师需要使用电路板设计软件来设计电路板,同时也需要考虑到性能和功耗等因素。
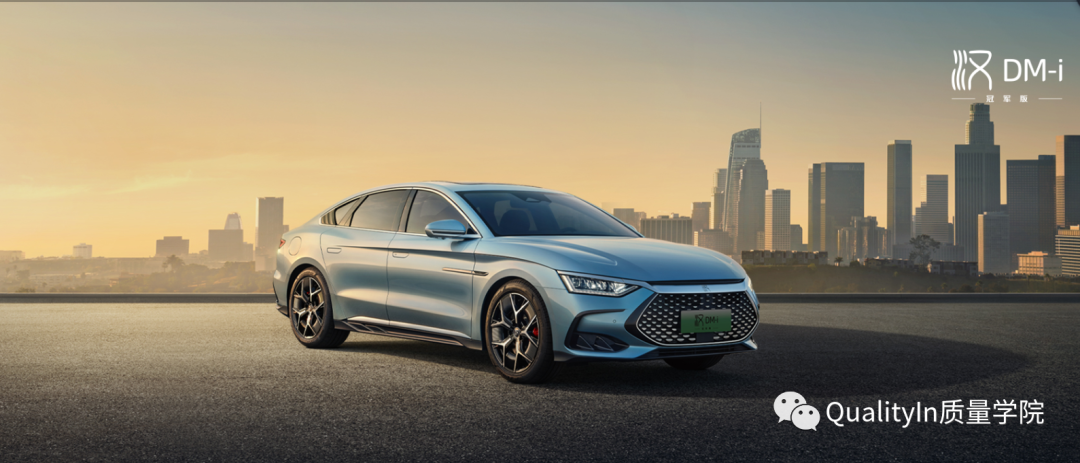
2、生产阶段
生产阶段是整个比亚迪电动汽车制造过程中最为复杂的一部分。在这个阶段中,比亚迪需要采用各种材料和设备来生产出汽车的各个组成部分,并进行组装和测试。
材料准备
在生产阶段之前,比亚迪需要准备大量的材料。这些材料包括各种塑料、金属、玻璃等原材料,以及各种电子元器件等。这些原材料需要经过一系列的加工处理,才能够成为汽车的组成部分。
电路板制作
电路板的制作是整个生产过程中最为关键的一环,需要经过多道工序才能完成。电路板制作的主要步骤包括图形设计、印刷、化学蚀刻、钻孔和电镀等。这些工序需要精确的操作和控制,以确保电路板的质量和性能。比亚迪通常会使用专门的设备和机器来完成这些工序。
在图形设计阶段,比亚迪的设计师会使用电路板设计软件来设计电路板的布局和元器件的位置。然后,这些设计图纸会被传输到印刷机上,进行印刷。在印刷完成后,比亚迪会使用化学蚀刻技术将不需要的部分蚀刻掉,留下需要的电路板图案。
接下来,比亚迪会进行钻孔,以便在电路板上安装元器件。最后,比亚迪会进行电镀,以便在电路板上形成导电层,连接各个元器件。
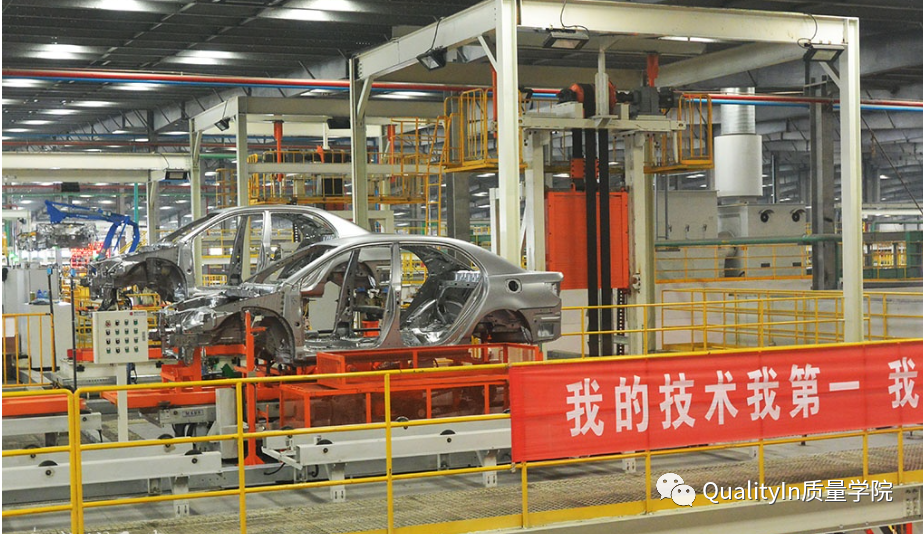
组装过程
在比亚迪的生产线上,组装是一个复杂而又严密的过程。汽车的电池、电机和电子控制单元是最为重要的组件。电池的制造需要先制备出电池的正负极片,再进行卷绕和注液,最后进行电池组装。电机的制造需要使用特殊设备来进行制造和组装,包括转子、定子、轴承等部件。而电子控制单元则需要对控制芯片进行程序编写和测试,并与电机和电池进行连接和调试。
测试和质量控制
在比亚迪生产出汽车后,需要进行各种测试,以确保其性能和质量。这些测试包括硬件测试、软件测试和安全测试等。硬件测试包括电池寿命测试、摄像头测试、屏幕测试等。软件测试包括操作系统测试、应用程序测试等。安全测试则包括数据保护测试、密码保护测试等。
在测试完成后,比亚迪需要进行质量控制。质量控制包括外观检查、尺寸测量、功能测试等。如果出现问题,比亚迪需要进行修复或替换。
二、特斯拉的电动汽车制造流程
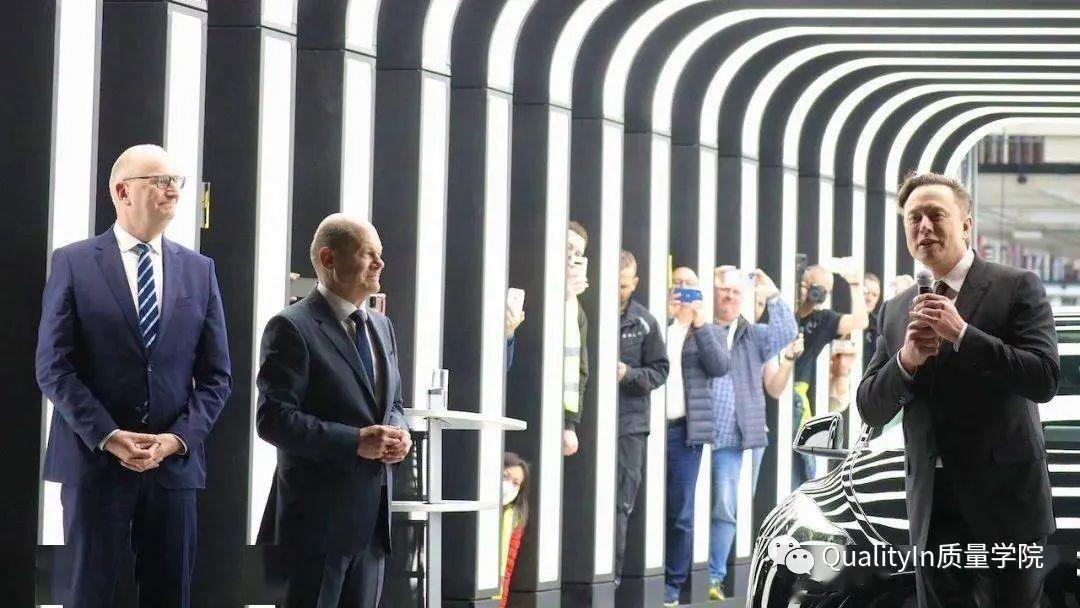
一、设计阶段
特斯拉的电动汽车设计过程也包括外观设计和内部结构设计。特斯拉的外观设计也是由著名工业设计师来负责。在设计过程中,特斯拉会使用先进的计算机辅助设计软件和仿真工具来模拟和测试汽车的外观和性能。特斯拉也会对汽车的空气动力学特性进行深入研究,以提高汽车的能效和舒适性。
对于内部结构设计,特斯拉采用了先进的一体化设计思想。特斯拉的设计师会设计出一整套一体化的电池、电机、电子控制单元和底盘等,以实现最佳的整车性能。同时,特斯拉也会在内部结构设计中考虑到舒适性、便利性和安全性等因素。

二、生产阶段
特斯拉的生产过程同样也是一套高科技生产流程。在生产阶段中,特斯拉采用了先进的机器人和自动化生产设备,以提高生产效率和产品质量。
电池制造
特斯拉的电池制造采用了自主研发的先进技术。特斯拉的电池采用了锂离子电池技术,具有更高的能量密度和更长的寿命。特斯拉的电池制造过程包括电池材料的制备、电极的制备、电池的组装和测试等步骤。特斯拉的电池制造过程也是非常严格的,需要精确的工艺控制和质量管理。
汽车组装
在特斯拉的生产线上,汽车组装采用了先进的机器人和自动化生产设备。特斯拉的汽车组装过程是一套高度自动化和精密的流水线生产过程,可以实现高效、高品质的汽车组装。特斯拉的汽车组装也包括多个生产阶段,包括焊接、涂装、装配等。
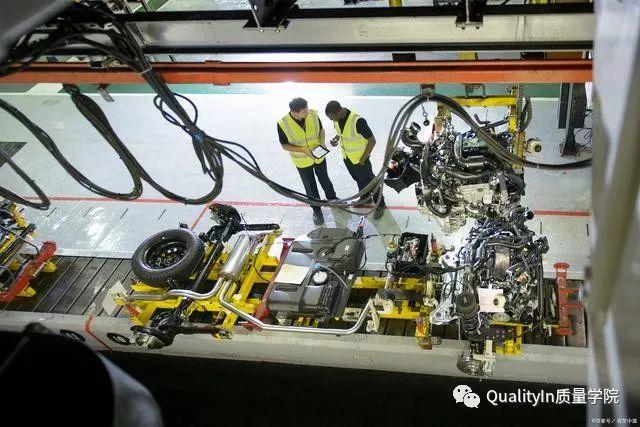
测试和质量控制
在特斯拉的汽车组装完成后,需要进行各种测试,以确保其性能和质量。这些测试包括硬件测试、软件测试和安全测试等。特斯拉采用了先进的测试设备和方法,以确保其汽车达到最高标准的质量和性能要求。
在测试完成后,特斯拉还需要进行质量控制。特斯拉的质量控制包括外观检查、尺寸测量、功能测试等。特斯拉还采用了独特的数字化制造技术,可以追踪每个部件的生产和质量数据,以确保每个汽车的质量和性能达到最佳水平。特斯拉的数字化制造技术也可以提高生产效率,降低成本和提高生产灵活性。
三、比亚迪和特斯拉的制造流程比较
比亚迪和特斯拉都是知名的电动汽车制造商,其制造流程具有许多相似之处,也有许多不同之处。
设计方面,比亚迪和特斯拉都采用了先进的计算机辅助设计软件和仿真工具。在外观设计方面,比亚迪和特斯拉都雇用了著名的工业设计师来负责。在内部结构设计方面,比亚迪和特斯拉的差异较大,比亚迪采用了传统的电动汽车组装方式,而特斯拉则采用了一体化设计思想,使得整车性能更加优越。
在生产方面,比亚迪和特斯拉的制造流程也有许多相似之处。比如都需要准备大量的材料,并使用各种设备和机器来加工和组装。但是特斯拉采用了更加先进的自动化生产设备和数字化制造技术,使得生产效率更高,产品质量更加稳定。特斯拉的制造过程还更加可持续,通过减少能源和材料的浪费,实现了更高的生产效率和更低的环境污染。
在测试和质量控制方面,比亚迪和特斯拉都采用了严格的测试和质量控制程序,以确保产品达到最高标准的质量和性能要求。但是特斯拉采用了更加先进的测试设备和方法,并通过数字化制造技术实现了更加精准的质量控制和生产数据分析。